|
|
|
Magnetic Abrasive Finishing (MAF) of Flat thrust bearing surfaces and cylindrical shafts for ultra high speed cryogenic applications Nair R. Sandeep1, Menon Rajendran S.1, Singh Trilok1 1Cryo-Technology Division, Bhabha Atomic Research Centre, Trombay, Mumbai-400 085 Abstract Nano-finishing of flat thrust bearing and cylindrical shaft surfaces employed in ultra high-speed cryogenic applications with Magnetic Abrasive Finishing (MAF) would reduce friction, minimize wear and increase service life. A magnetic field applied across the machining gap containing a homogeneous mixture of abrasive (diamond paste (5 μm) and ferromagnetic iron particles), aligns the ferromagnetic particles to form a flexible magnetic abrasive brush (FMAB). A novel MAF setup has been developed that can finish both cylindhcal and flat surfaces. The FMAB can move in longitudinal direction as the workpiece rotates and can finish a cylindrical shaft to a roughness value of 0.023 μm (23 nm) Ra. A fiat bearing surface was also finished to a roughness value of 0.029 μm Ra and flatness value of about 5 μm with transverse feed of FMAB. Effects of such improvements in surface finish and flatness values on the performance of the rotor-bearing assembly are being studied. Top Keywords Magnetic abrasive finishing, MAF, Ultra high speed shafts, Thrust bearings. Top | INTRODUCTION Turbo-expanders consisting of ultra high speed shafts (rotors) and thrust bearings are employed in cryogenic applications like helium refrigerators and liquefiers. Since the turboexpander rotational speed is of the order of 4000 Hz or more, the shafts and bearings are subjected to fatigue and wear due to friction. This reduces the service life of the unit and hence friction has to be minimized as much as possible. If starting friction is high, starting torque and wear will be considerable. |
Friction between bearing and shaft as well as shaft collar and thrust bearing surfaces can be reduced considerably if the surfaces have a very low value of surface roughness, Ra [1, 2], Also, if the flatness values of thrust bearing surface and shaft collar are very low, good parallelism is obtained. This helps in maintaining rotor bearing clearances with optimum stiffness resulting in better dynamic characteristics of the rotor. Cylindricity of the shaft and flatness of the bearing surface is very critical since they affect the rotor dynamics. These elements of form geometry can be maintained by conventional machining like turning and grinding. Further improvement of cylindricity is not easily possible by finishing methods. However, improvements in flatness are possible by some non conventional finishing methods. When the roughness peaks of the surface is brought to the same level by finishing, flatness and Ra values improve. |
Top MAGNETIC ABRASIVE FINISHING (MAF) Magnetic Abrasive Finishing (MAF) is a finishing technique that can be successfully employed to obtain high surface finish on cylindrical shafts and thrust bearing surfaces. MAF minimizes the formation of micro-cracks on the work piece surface, which is essential for practical applications where fatigue failure is minimized. In this process, a magnetic field is applied across the machining gap (between the magnet and work piece) filled with unbounded magnetic abrasive powder (UMAP), i.e. a homogeneous mixture of abrasive (Diamond paste, 5 pm grit size) and ferromagnetic iron particles. |
In MAF, the ferromagnetic particles get aligned along the magnetic lines of force and form a flexible magnetic abrasive brush (FMAB), which originates micro indentations into the work piece surface [3, 4], The brush is flexible and can access surfaces where conventional tools are hardly applicable in practical use. This process is based on the magnetization property of ferromagnetic iron and the machining property of the abrasives used. Ferromagnetic materials like steel, as well as nonferromagnetic materials including stainless steel and brass can be finished up to nano level surface roughness by this process [5, 6], |
MAF has various applications such as deburring operations, finishing of internal as well as external cylindrical surfaces and finishing of flat surfaces. The major research areas in the subject include process and parametric studies, development of new processes and a new set of abrasives. Modeling and simulation studies can also be found in literature [7-10]. Research work in the area of mass finishing has not been much explored. An attempt has been made however, to finish two workpieces simultaneously to the same level of surface roughness, Ra using MAF [11], |
In the work reported in this paper, a novel setup has been developed wherein both cylindrical and flat surfaces can be finished using MAF with appropriate fixtures. The effects of such improvement in surface finish and flatness values on the performance of the rotor-bearing assembly are being studied. Starting friction and torque values are expected to be much lower. |
Top MAF SETUP Figure 1 shows the schematic of the MAF setup used for finishing of shafts and thrust bearings. The setup has a lathe machine base with an appropriate fixture used instead of the cutting tool. Different fixtures and permanent magnets have to be used depending on the work piece to be finished. Movement in both transverse and longitudinal directions is possible for the FMAB (Figure 2) as the work piece rotates. The MAF setup consists of the following components: (1) Lathe machine (2) Tool Post modified to hold magnet fixture (3) Magnet fixture (4) Permanent magnet (5) Magnetic abrasive paste (used as media) and (6) Work piece. |
The lathe, when put in lower gear, can rotate the workpiece from a speed of 200 RPM to 1500 RPM. The magnet fixture used is decided based on the workpiece to be finished. The magnet is concave in shape when used for finishing external cylindrical surfaces like shafts and is circular in shape when used for flat surfaces like thrust bearings. Only the magnet and fixture need to be altered when either shaft or the thrust bearing is to be finished. The permanent magnet used has a magnetic flux intensity of about 0.3 T (3 kG). |
Hence gap maintained between the magnet and workpiece surface should be minimum so that stronger magnetic field is obtained in the working gap. |
The magnetic abrasive paste, i.e. MAF media used consists of Iron particles and abrasive paste. Iron particles (Mesh Size 300) and abrasive Diamond paste (5 μm grit size) were taken and mixed in the ratio 3:2 by volume to make the media. Specific Gravity of Iron particle and Diamond paste Abrasive are 7.6 and 3.5 respectively. Diamond paste is self lubricating and helps in adhesion of small Diamond grains on iron particles. The magnetic forces not only concentrate the iron particles in the working gap where magnetic field strength is superior, but also prevent them from splashing due to work piece rotation. The congregated iron particles form a magnetic brush along the line of magnetic force within the working gap, which causes pressure on the work surface. This pressure will act on the Diamond abrasive beneath the iron particles, to generate abrasion. The abrasive cannot perform the cutting task unless it obtains abrasion pressure from the iron particles. For abrasive treatment to be effective, the iron particles must be prevented from not only splashing out of the working gap, but also rolling therein [12]. |
Top MAF EXPERIMENTS The preliminary experiments were conducted on the setup using One Factor At a Time (OFAT) technique. The parameters that can be studied for the MAF setup are taken into consideration and OFAT is conducted with each parameter. The various parameters in MAF are: (1) Rotational Speed of workpiece(2) Working Gap (3) Abrasive Grit Size (4) Magnet Feed (5) Finishing time and (6) MAF media composition. Among all these parameters only the first five turned out to be majorly influential. Finishing time however was taken as a fixed parameter for all the experiments so that individual effects of each parameter could be studied. Initial surface roughness, Ra was taken as 0.2±0.05 pm for carrying out the experiments. Final roughness value Ra was observed for each experiment. |
Figure 3 shows the variation of surface roughness, Ra with rotational speed of the workpiece. It is observed that with increase in speed, surface roughness value decreases. This is because the abrasive is able to remove more surface peaks and thereby improve surface finish. |
Ra reaches its lowest value at 1100 RPM speed. With further increase in speed beyond 1100 RPM, the force of rotation exceeds the magnetic force holding the brush and hence the brush disintegrates. Most of the abrasive gets splashed away and the remaining abrasives start rubbing action with workpiece and worsen the surface finish. Hence, there is an optimum value of rotational speed beyond which MAF is ineffective for the setup. |
It is observed in Figure 4 with decrease in working gap, i.e. gap between the magnet pole and workpiece surface, surface roughness value decreases. Ra reaches its lowest value at 1 mm gap. As gap reduces, the magnetic brush becomes stronger since at small gap there is higher magnetic flux. With increased brush density, more abrasives are able to remove the surface peaks and thereby improve surface finish. Ra reaches its lowest value at 1 mm gap. With further decrease in gap below 1 mm, there is insufficient amount of abrasive left for finishing the workpiece surface. The remaining abrasives start rubbing action with workpiece and worsen the surface finish. Hence there is an optimum working gap to be used for the MAF setup. |
In Figure 5 it is observed that by using finer grit size abrasive, surface roughness value decreases. Coarser grit size abrasive removes larger surface peaks on the workpiece surface. As grit size is reduced, even smaller surface peaks are sheared off thereby improving surface finish. Abrasive should be used such that coarser grit size is used first for rough finishing and later on finer grit size for fine finishing. The lowest possible Ra value achievable with the setup depends on the finest grit size abrasive employed for MAF. |
In Figure 6 it is seen that by increasing magnetic brush feed in transverse direction, surface roughness value decreases. With slow feed there is better contact between abrasive and workpiece surface, although material removal is slower. With increase in feed, more abrasives come in contact with the surface and more surface peaks are sheared off due to increased relative motion between workpiece and brush. Hence surface finish improves with moderately high feed of magnetic brush. |
Top RESULTS AND DISCUSSION For sample finishing using the setup, initial roughness values for flat and cylindrical surfaces were taken as 0.1 μm (100 nm). Using 5 pm grit size Diamond paste, the setup is capable of finishing a cylindrical shaft to a final roughness value of 0.023 μm (23 nm). A flat bearing surface was also finished to a final roughness value of 0.029 μm (29 nm) and flatness value of about 5 μm from an initial 14 pm (Figs. 7&8). |
While testing the above shaft-bearing assembly of turbo-expander in experimental cold box setup, (a) It was found that minimum gas pressure needed to start the rotation of the shaft decreased to a value of 0.8 bar (gauge) and (b) In normal operation, when the shaft is not finished by MAF, gas pressure needed to start rotation of shaft is 1.2–1.4 bar (gauge). Drop in starting pressure indicates the reduction in friction and torque considerably due to improvement in surface finish of shaft and bearing by MAF process. |
Top CONCLUSIONS By finishing the rotor-bearing assembly using MAF, starting friction and torque requirement for the unit was found to decrease. It is expected that an improvement will be seen in the dynamic characteristics of the rotor-bearing system. Some noticeable observations were: |
Rotational Speed was found to substantially influence the surface finish obtained by MAF process and hence needs to be optimized for different setups. Working gap should also be optimized for different setups to obtain best value of Ra- With use of finer abrasive grit size, even lower values of Ra are attainable. Feed has the least influence among the machine parameters although a moderately high feed is essential so that chips formed are removed periodically from the workpiece surface without deteriorating surface finish. Further studies can be done to find out the combined effects of these parameters on surface finish. It has also been observed that on flat surfaces, multiflatness values can be substantially improved by MAF, provided the initial flatness value is high.
Top ACKNOWLEDGEMENTS The authors would like to acknowledge their colleagues at Cryo-Technology Division, BARC, for their help in timely completion of the experiments. |
Top Figures Figure 1: Schematic MAF Setup
| 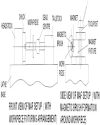 | |
| Figure 2: FMAB generation in MAF setup
| 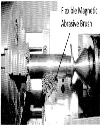 | |
| Figure 3.: Variation of surface roughness, Rawith Rotational Speed
| 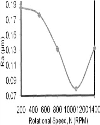 | |
| Figure 4.: Variation of surface roughness, Rawith Working Gap
| 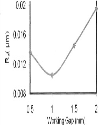 | |
| Figure 5.: Variation of surface roughness, Rawith Abrasive Grit Size
|  | |
| Figure 6.: Variation of surface roughness, Rawith Feed
| 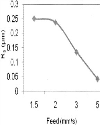 | |
| Figure 7.: Surface roughness readings of flat bearing surface (a) before MAF (initial Ra = 0.1 μm) and (b) after MAF (Final Ra = 0.029 μm)
| 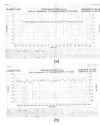 | |
| Figure 8.: Multiflatness readings of flat bearing surface (a) before MAF (Multiflatness = 14.94 μm) and (b) after MAF (Multiflatness = 5.515 μm)
| 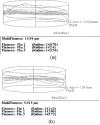 | |
|
| | |
|
|
|