|
|
(3.144.40.64)
|
Users online: 10591
|
|
|
|
|
|
Ijournet
|
|
|
|
|
Development and performance tests of miniature stirling cryocooler Jadhav Mohananand1, Menon Rajendran1, Singh Trilok1 1Cryo-Technology Division, Bhabha Atomic Research Centre, Mumbai, 400085 Abstract This paper is about development of a gamma-type integral Stirling cryocooler. The cryocooler consists of piston, displacer, regenerator, Dewar, clearance seals, and rotary BLDC motor. The design was targeted for applications such as night vision device where compactness and light weight design are prime requirements. These requirements make design of piston, cylinder, and clearance seals very critical. Assembly procedures require particular attention while handling precise components. Helium filling requires a special fixture and procedures to avoid contamination.A BLDC motor was developed to be used as prime mover for miniature cryocooler. Compactness and high efficiency make BLDC a proper choice. The prototype Stirling cryocooler has been tested and parameters such as power consumption, coefficient of performance are investigated under various rotating speeds and charged pressure, which will help us in further developments and optimization of cryocooler. Top Keywords Stirling Cryocooler, Infrared, Night vision, Piston-Cylinder, BLDC Motor. Top | INTRODUCTION Stirling cycle based cryocoolers are well suited for cooling of IR sensor and other electronics due to the advantage of being compact, light weight, low maintenance machine with fast cool down rates [1]. Stirling cycle machines are valve-less, making them more popular than other regenerator based cycle and are well documented by Walker [2], Most of the electronics cooling applications require refrigeration capacity of 0.25–2 W at around LN2 temperature. At this capacity, sizes come drastically down any way and specific applications require even more compactness. However with small sizes, temperature and pressure gradients become large thereby increasing the share of losses. |
Volume of gas leak through the piston cylinder clearance in each cycle also increases, becoming comparable to the total swept volume. This widely affects the pressure ratio and performance [3]. To counter all these effects, small clearances are must in these cryocoolers. Oil free process requirement makes operation with low clearances much difficult. Assembling these components require special attention. The cryocooler has to work as an independent unit, hence a Helium filling and sealing arrangement is necessary. Rotary motor are compact and particularly suitable for integral configuration of cryocoolers. Placing the motor inside the helium space makes the unit very compact but requires feed-through to supply current inside the hermetically sealed unit. Brush less direct current (BLDC) motors have advantages over brushed DC motors and induction motors. It has better speed versus torque characteristics, high efficiency, long operating life, noiseless operation and rugged construction [4] all of which makes it suitable for electronics cooling applications. |
Top DESCRIPTION OF THE CRYOCOOLER The cryocooler schematic is shown in Fig. 1. It is an integral construction, gamma type and based on Stirling cycle. Regenerator is housed inside the displacer. BLDC motor is used as prime mover. Crank and slider mechanisms are used to drive both piston and displacer. Common crank (eccentric) is used for this purpose; hence the phase angle is determined by positions of the sliding axis. Rotor part of the motor is installed inside the crank case and hermetically sealed while stator is outside the sealing. This compromises the compactness but reduces the complexity and need of feed through and associated failures. |
The cryocooler was designed to operate with 250mW of refrigeration at 77K. The motor was designed to operate with 12V DC power supply. Operating speed varies from 30Hz to 65Hz. Working fluid is Helium with filling pressure not more than 30 bar. Gas filling hole with sealing screw is located at the top of cryocooler crankcase. Piston diameter is 14mm and stroke length is 2.1mm. Displacer swept volume ratio between cold and hot side is 1.4. Displacer is made up of Nylon. It reciprocates inside a thin walled Titanium Tube. Regenerating material used is steel wire mesh having 76% porosity. |
Both compressor and displacer are isolated from crank case by means of clearance seals having 11 microns diametric clearance. To reduce wear and friction, male part of the clearance seals are coated with hard chrome and female parts have oxide layer on the surface. |
The developed BLDC motor consists of 3 pole pairs mounted on a hexagonal core. 3 hall sensors are used to sense the position of magnet which is used to energize particular windings distributed over 18 slots. |
Top RESULTS OF EXPERIMENTS AND TEST One of the critical components in the cryocooler is the clearance seal. For micro miniature cryocoolers [2], no cooling is achieved if the clearance exceeds 15 microns [3]. Various materials were tried for seals having dry sliding (∼0.5m/s) operation with low clearance. |
High strength aluminum with diamond like coating (DLC) with suitable intermediate coating (Fig. 3) has been found to be a good material. The performance was satisfactory with reduced weight and vibration. Steel piston with hard chrome coatings and hardened steel cylinder also had satisfactory performance along with advantage of simpler manufacturing process. |
Assembling of the components needs to be done in clean environment and even the presence of small dust can cause failures in the sliding part. Most of the components including the housing are made-up of aluminum. The assembling requires special tools and particular care while handling to prevent the scooping of aluminum particles by hardened assembly components. The presence of these particles in an assembled unit may cause failure due to stalling. |
Fig. 4 shows the test setup. Helium is filled in the unit through a purifier at required pressure. A tungsten heating filament is wrapped on the coldfinger. Current through the filament is varied to obtain different refrigeration loads. Semiconductor based temperature detector is cemented with coldfinger tip to monitor the temperature. Coldfinger is covered with vacuum jacket having vacuum better than 10−4 mbar. Both current and detector leads are taken out of the Dewar by feedthroughs. Supply to the motor winding is provided through a circuit which can chop the supply voltage at high frequency to manipulate the speed of motor. |
Motor was tested independently with a dynamometer. Fig. 5 shows the performance of the developed BLDC motor. Torque of magnitude greater than 12 N.mm is available at all speeds with efficiency generally better than 65%. |
The Cryocooler has been tested for speeds ranging from 30 Hz to 66 Hz. Output of the hall sensors of BLDC motor was used to measure the speed. Refrigeration is varied from 0 to 800 mW. Fig. 6 shows the performance of cryocooler at 30 bar filling pressure. The constant temperature lines can be seen almost parallel to constant COP lines. Cool down time from ambient was less than 7 min. |
Fig. 7 shows performance plotted on temperature-speed plane. From the graph it is observed that the Steady state temperature shows slight rise at higher speeds. The same is reflected in concavity of constant temperature lines with respect to COP lines in Fig. 6. This is due to increased frictional and shuttle heat losses at high speeds. Variation of steady state temperature with respect to speed and effect of filling pressure on it are shown in Fig. 8. |
Top CONCLUSION The cryocooler described was designed to provide 250 mW of refrigeration at 80K and cool down time less than 7min. It can be observed in the plot of Fig. 6 that at a speed of around 45Hz, refrigeration achieved is 400mW at 80K which is actually required to realize the desired cooldown time. Hence, it can be concluded that the cryocooler achieves its objective of desired cooling with good performance. It has been realized in the course of development and performance evaluation that clearance seals with hard chrome coating constitute one of the most important components in achieving this performance. Performance and reliability can be further improved with DLC coating. Further development option can be DLC coated clearance seals with flexural spring support (similar to linear motor compressors). The cryocooler was operated for a total of 200hrs in the laboratory for performance evaluation. Further experiments are required to evaluate the reliability. |
Top ACKNOWLEDGEMENT Efforts by CrTD staff Shri. J. Tambe, Shri S. Patil and Shri D. Bhosle, towards completion of the cryocooler experiments are greatly acknowledged. |
Top Figures Fig. 1.: Schematic of Integral Stirling Cryocooler
| 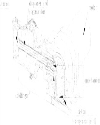 | |
| Fig. 2.: Nylon Displacer with Regenerator
| 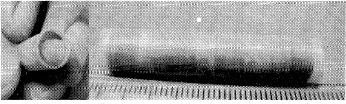 | |
| Fig. 3.: Clearance Seal (Al), DLC coated Piston, Hard Chrome coated Piston.
| 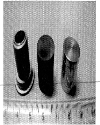 | |
| Fig. 4.: Cryocooler Test Setup
|  | |
| Fig. 5.: Performance of BLDC Motor
| 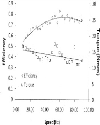 | |
| Fig. 6.: Cryocooler Performance at 30bar.
| 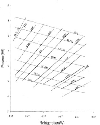 | |
| Fig. 7.: Temperature variation with respect to speed at 30 bar filling pressure
| 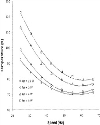 | |
| Fig. 8.: Temperature variation with respect to speed at 250mW Refrigeration
| 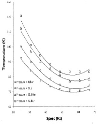 | |
|
| | |
|
|
|
|
║ Site map
║
Privacy Policy ║ Copyright ║ Terms & Conditions ║
|
|
751,605,624 visitor(s) since 30th May, 2005.
|
All rights reserved. Site designed and maintained by DIVA ENTERPRISES PVT. LTD..
|
Note: Please use Internet Explorer (6.0 or above). Some functionalities may not work in other browsers.
|