A Comparative Study of Performance, Combustion and Emissions of Diesel, Jatropha Methyl Ester and Karanj Methyl Ester in a DI-CI Engine Jindal S.1,*, Nandwana B.P.1, Rathore N.S.2 1Mechanical Engineering Deptt, College of Technology & Engineering, Udaipur 2Renewable Energy Sources Deptt, College of Technology & Engineering, Udaipur *Email ID: sjindals@gmail.com
Abstract Biodiesel produced from different vegetable oils and fats are likely to have some comparative advantages and disadvantages. Two major oil varieties, considered suitable for biodiesel making are ‘Jatropha curcas’ and ‘Pongamia pinnata’. This study targets at making a comparison of the methyl esters of these oils in a diesel engine vis-à-vis diesel fuel. The performance of the fuels was evaluated in terms of thermal efficiency, specific fuel consumption, power output and mean effective pressure, cylinder pressure, rate of pressure rise and heat release rates. The emissions of carbon monoxide (CO), carbon dioxide (CO2) unburnt hydrocarbon (HC), oxides of nitrogen (NOx) and Smoke opacity with the three fuels were also compared. Both the varieties of the oil, after transesterification, exhibit the major properties within acceptable limits of biodiesel standards set by many countries. Karanj methyl ester (KME) performed better than Jatropha methyl ester (JME) whereas shortest ignition delay is observed with JME. Both the esters performed poorer than diesel but emissions ofHC, NOx and smoke were found lower with esters. The three fuels delivered almost same brake power even when the indicated power was higher with diesel. Top Keywords Jatropha methyl ester, Karanj methyl ester, Thermal efficiency, BSFC, Heat release rate, Emissions. Top |
Introduction For diesel engines, as a significant research effort has been directed towards using vegetable oils and their derivatives as fuels. There exists number of vegetable/plant, which produces oil and hydrocarbon substances as a part of their natural metabolism. These vegetable oils from oil seeds crops like soybean, sunflower, groundnut mustard etc. and oil seed from tree origin have got 90 to 95% energy value of diesel on volume basis, comparable, cetane number and can be substituted 20–100%. |
Biodiesel is considered as a promising alternative fuel for use in diesel engines, boilers and other combustion equipment. Compared to fossil diesel fuel, biodiesel has several superior combustion characteristics. Although biodiesel has many advantages over diesel fuel, there are several problems that need to be addressed such as its lower calorific value, higher flash point, higher viscosity, poor cold flow properties, poor oxidative stability and sometimes its comparatively higher emission of nitrogen oxides [1]. Biodiesel obtained from some feed stocks might produce slightly more oxides of nitrogen (1–6%), which is an ozone depletor, than that of fossil origin fuels but can be managed with the utilization of blended fuel of biodiesel and high speed diesel fuel [2]. It is found that the lower concentrations of biodiesel blends improve the thermal efficiency. Reduction in emission and brake specific fuel consumption is also observed while using B10 [3]. Most of the research studies concluded that in the existing design of engine and parameters at which engines are operating, a 20% blend of biodiesel with diesel works well [3]. |
Biodiesel made from different feed stocks have been tried by many and the effect of feedstock on engine performance and emissions are well documented. Two of the major feedstock researched in India are ‘Jatropha’ and ‘Karanj’. Looking to the availability and their biodiesel potential, these oils are becoming more and more popular in many other countries as well. Evaluation of Jatropha esters [4] and Karanj esters [5] indicates their superiority over many other vegetable oils in terms of engine performance, emissions, ease of use and availability. All of the studies made so far with these oils were independently done in different types of engines in different conditions. An effort is made in this study to compare the combustion, engine performance and emissions with the methyl esters of these oils in one engine keeping all other conditions same for establishing the suitability of these esters against the diesel fuel. |
Jatropha curcas, locally known as ratanjyot, belongs to the family of Euphorbiaceae. It is a quick yielding plant that survives in degraded, barren, forest land and draught prone areas and is cultivated as hedge on the farm boundaries (Figure 1). The de-oiled cake is excellent organic manure which retains soil moisture. This oil is gaining popularity due to its good properties and has been accepted and recommended by National Biodiesel Board of India [6] as a source of alternative fuel for blending in the commercial diesel. Karanja (Pongamia pinnata) is an underutilized plant which is grown in many parts of India (Figure 2). Sometimes the oil is contaminated with high free fatty acids (FFAs) depending upon the moisture content in the seed during collection. It is a fast growing leguminous tree with the potential for high oil seed production and the added benefit of an ability to grow on marginal land. These properties support the suitability of this plant for large scale vegetable oil production needed for a sustainable biodiesel industry. The potential of Jatropha oil [7-9] and Karanja oil [10-12] as a source of fuel for the biodiesel industry is well recognized. |
Top Experiment and Procedure In the study, the selected two vegetable oils were transesterified and the effect on major properties was evaluated. Further, the evaluation of the two methyl esters was done in a compression ignition engine for combustion, performance and emissions. The results were compared against the diesel fuel results. |
Transesterification The transesterification of these oil samples was carried out in the lab using standard procedures adopted commonly through out the world [13]. As Jatropha oil contains low FFA (less than 5%), methanol with KOH as catalyst was used. For Karanj oil (FFA more than 5%), the FFA was reduced first by acid catalysed esterification (using methanol in presence of sulphuric acid) and then alkali catalysed esterification (using methanol in presence of KOH) was done. After separation of glycerol, the ester was water washed to remove un-reacted methoxide. It was then heated to remove the water traces to obtain clear biodiesel. The methyl ester (biodiesel) thus produced by this process was totally miscible with mineral diesel in any proportion. The properties of so prepared biodiesel were tested in the laboratory and are listed in table 1. Experimental Set-Up The study was carried out in the laboratory on an advanced fully computerised experimental engine test rig comprising of a single cylinder, water cooled, four stroke diesel engine, commonly used in agriculture sector for minor irrigation needs, connected to eddy current type dynamometer for loading. The setup (Figure 3) includes necessary instruments for online measurement of cylinder pressure, injection pressure and crank-angle. The specifications of the engine are given in table 2. The exhaust gases were sampled from exhaust line through a specially designed arrangement for diverting the exhaust to sampling line without increasing the back pressure and was then analysed using a portable multi-gas analyser (make- MRU Airfare, Germany; Model- DELTA 1600 S). It measures carbon monoxide (CO), carbon dioxide (CO2), hydrocarbons (HC) and Nitric Oxide (NO). For the measurement of smoke intensity (percent opacity HSU) of diesel engine's exhaust, a diesel smoke meter (model- DSM 2000; make- Manatee Electronics) was used. Experimental Procedure The performance test of the engine was conducted with standard diesel, Jatropha methyl ester and Karanj methyl ester. The engine was tested at no load and at 25, 50, 75, 100 and 125 percent loads. The experiment was replicated three times. For all settings, the emission values were recorded thrice and a mean of these was taken for comparison. The performance of the engine at different loads and settings was evaluated in terms of brake thermal efficiency (BTHE), brake specific fuel consumption (BSFC), indicated (IP) and brake power (BP), exhaust temperature, indicated mean effective pressure (IMEP), cylinder pressure (Pc), rate of pressure rise (dP/dθ), net heat release rate (dQn/dθ) and emissions of carbon monoxide (CO), carbon dioxide (CO2), un-burnt hydrocarbon (HC) and oxides of nitrogen (NOx) with exhaust gas opacity. Top Results and Discussion Brake Thermal Efficiency The brake thermal efficiency obtained with diesel was higher than that obtained by both of biodiesel (Figure 4). KME gave consistently higher BTHE than JME over entire load range. The viscosity of KME is lower than that of JME and hence better combustion takes place which is also indicated by comparatively higher exhaust temperature and lower BSFC. At full load, the BTHE values for diesel, JME and KME were found to be 26.49, 22.69 and 24.03 percent respectively. The smaller differences in BTHE at lower loads tend to increase with increase in load. Brake Specific Fuel Consumption The brake specific fuel consumption with diesel fuelling was lower than that for the other two fuels as shown in figure 4. The BSFC values for diesel, JME and KME at full load were 0.29, 0.39 and 0.34 Kg/KW-hr respectively. It is seen that the difference between BSFC of diesel and biodiesel is larger at lower loads as compared to full load. This is due to the fact that the esters of vegetable oils have lower heat value when compared to diesel and therefore more biodiesel is needed to maintain the power out-put. Similar findings are reported by other researchers also. The BSFC for KME is lower as compared to JME as the relative density of KME is lower than that of JME and hence lesser mass of KME fuel is injected in same volume. Exhaust Temperature Temperature of exhaust gases, leaving the cylinder, represents the extent of temperature reached in the cylinder during combustion. With increasing load, the cylinder pressure increases and more of the fuel is burnt leading to increase in temperature. The temperature of exhaust gases is observed to be higher with B0 as compared to B100 for entire load range (Figure 4). This is expected as the heat contents of B0 are more than B100 and greater amount of heat is released in combustion chamber leading to higher temperature. Also the heat released by combustion of diesel is late by few degrees and thus more heat gets exhausted. The temperature of exhaust gases obtained with JME were lowest followed by KME. The temperature of exhaust at full load for JME, KME and diesel were 383, 393 and 427°C respectively. Power and Mean Effective Pressure The indicated power developed by engine with diesel fuel is also found to be higher than that of the biodiesel (Figure 5) similar to the results of indicated mean effective pressure development. The indicated power developed with KME is slightly higher than that developed by JME above 50 percent load. At full load. JME and KME developed 5.09 and 5.19 kW respectively whereas diesel developed 5.41 kW of indicated power i.e. loss of 6% and 4% respectively with esters. The mean effective pressures at full load for diesel. JME and KME are 6.49, 6.09 and 6.17 bar respectively. The mean effective pressure with JME is lower by 6.2% and with KME, loss of 5% is observed. Brake power of the engine is almost same (little higher) for all fuels indicating better mechanical efficiency with esters as frictional losses are lower due to higher lubricity of these fuels. Rate of Pressure Rise and Net Heat Release Rate The pressure in the cylinder during the cycle is found to be almost same for both methyl esters and diesel. The rate of pressure rise for full load is found to be highest with diesel fuel as compared to other fuels but the biodiesel fuels- JME and KME shifts the peak pressure rise rate towards the top dead centre (TDC) with reduced ignition delay. The peak rate of pressure rise with diesel, JME and KME were found as 4.79, 4.02 and 3.82 bar/CA respectively. KME advances the peak pressure rise rate position more (4°) as compared to JME (2°) because of its higher volatility. The ignition delay is shortest with JME (5°) followed by KME (7°) and diesel (8°) The shift is mainly due to advancement of injection due to higher viscosity and earlier combustion due to higher cetane number of these fuels (Figure 6)Similarly, the peak net rate of heat release (NHR) is lower for JME (42.14 J/CA) and KME (39.86 J/CA) as compared to diesel (53.95 J/CA) but earlier heat release is obtained with biodiesel. Emissions The emission parameters for different fuels measured at full load are shown in figure7 and 8. The Unburnt hydrocarbon emission (UHC) is highest for diesel (Figure 7). With JME and KME as fuel, UHC emissions are reduced by 56% and 40% respectively. The reasons for reduction in UHC as reviewed by Lapuerta et al. [14] are: higher oxygen content (leading to more complete combustion), higher cetane number (reducing combustion delay), higher final distillation point for diesel (final fraction may not vaporize) and advanced injection and combustion timing. Measured CO emissions are lowest with KME and highest for JME (Figure 7). The CO emissions are higher for JME by 38.4% and lower for KME by 23% as compared to diesel. During the combustion, HC is first converted into CO and than into CO2, thus, a trade-off between UHC and CO is expected. With larger amount of UHC sent to exhaust, better availability of oxygen is ensured for remaining fuel leading to complete combustion. JME emits lesser UHC as compared to KME and hence CO emissions for JME are higher than KME. Similarly, emissions of CO2 are also highest with JME and lowest with KME (Figure 7). The CO emissions with diesel, JME and KME at full load are 4.6, 4.7 and 4.4 percent respectively. The reduced UHC emission with JME and higher emissions of CO and CO2 shows better conversion of hydrocarbons into oxides of carbon. The smoke opacity of engine exhaust (Figure 8) is lower by 20% with JME and 41% with KME as compared to diesel exhaust. The reason for reduction in smoke opacity (or particulate matter) is again higher oxygen contents of biodiesel molecule, which enables more complete combustion even in regions of the combustion chamber with fuel-rich diffusion flame promoting the oxidation of the already formed soot [15]. The measured values of NOx emissions with JME and KME are lower than that with diesel (Fig 8). With JME the reduction is 25% where as with KME the reduction is 48%. At full load JME and KME emitted 178 and 147 ppm of NOx against 237 ppm of NOx with diesel. The decrease in NOx emissions with biodiesel has been reported by many others also. Graboski et al. [16] indicated a linear relationship between NO emission and iodine number of the fuel being tested. As the iodine value of KME is lower than that of JME, decrease in NOx emissions is expected. Top Conclusions During engine trials, KME gave better thermal efficiency and specific fuel consumption than JME, but both ester fuels performed poorer than diesel. The BTHE for diesel, JME and KME at full load is found as 26.49, 22.69 and 24.03% and BSFC as 0.29, 0.39 and 0.34 kg/kW-hr respectively. The exhaust temperature was 427, 383 and 393°C and indicated power developed was 5.41, 5.09 and 5.19 kW whereas brake power was almost same for all fuels indicating lower losses with esters. The peak rate of pressure rise is highest with diesel but position of peak rate with esters advances with larger amount of heat release in mixing controlled combustion regime. KME shifts more as compared to JME. The emissions of UHC, NOx and smoke opacity are found highest with diesel. About 50% reduction in UHC, 25% reduction in NOx and 20% reduction in smoke opacity is observed with ester fuels. CO and CO2 emissions were higher with JME and lower with KME when compared to diesel emission. |
Top Figures Figure 1.: Plant, fruit and seed of Jatropha curcas
| 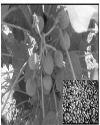 | |
| Figure 2.: Tree, fruit and seed of Karanj
| 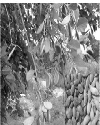 | |
| Figure 3.: Engine test setup
| 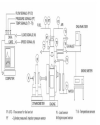 | |
| Figure 4.: BTHE, BSFC and Exhaust temperature v/s Load for different fuels
| 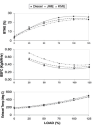 | |
| Figure 5.: IMEP, Indicated and Brake Power v/s Load for different fuels
| 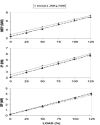 | |
| Figure 6.: Cylinder pressure, Rate of pressure rise and Net heat release rate (full load)
| 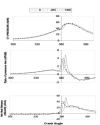 | |
| Figure 7.: Emissions of unburnt Hydro carbon, Carbon monoxide and Carbon dioxide at full load for different fuels
| 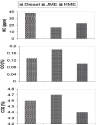 | |
| Figure 8.: Emissions of unburnt Oxides of Nitrogen and Smoke at full load for different fuels
| 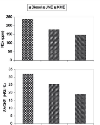 | |
|
Tables Table 1:: Properties of diesel and methyl esters
| Property | Unit | Diesel | Jatropha Methyl ester | Karanj Methyl Ester | Relative density | gm/cm3 | 0.8394 | 0.8838 | 0.8749 | Calorific value | MJ/kg | 44.13 | 39.40 | 39.19 | Kinematic Viscosity | | | | | at 32°C | cSt | 3.93 | 10.8 | 7.52 | at 60°C | cSt | 2.77 | 5.82 | 3.2 | Cloud Point | °C | <3 | 0 | 2 | Pour Point | °C | <-5 | -3 | -2 | Flash Point | °C | 56 | 118 | 122 | FFA | % | - | 0.28 | 0.50 | Iodine value | | - | 100.01 | 82.66 |
| | Table 2:: Test engine details
| Make | Kirloskar | Model | TV1 | Details | Single cylinder, DI, Four stroke | Cooling | Water | Bore and stroke | 87.5mm × 110 mm | Cubic capacity | 0.661 liters | Compression ratio | 17.5:1 | Rated power | 3.5 kW at 1500 rpm | Load at rated power | 12 kg | Injector opening pressure | 210 bar | Peak pressure | 77.5 kg/cm2 | Injection timing | 23° BTDC static (diesel) | Modified compression ratio range | 12 to 18 |
| |
|