|
|
|
Production of Fuel Ethanol from Woody Biomass Jain Tushar1,*, Gerpen Jon Van1, McDonald Armando1 1University of Idaho, Moscow, Idaho, USA *Email ID: jain6843@vandals.uidaho.edu
Abstract The most abundant bioenergy feedstock in the world is lignocellulosic material. This material can be categorized in three main parts; agricultural, forestry and recycled materials. The key steps in lignocellulosic bioethanol production are pretreatment, enzymatic hydrolysis, fermentation and recovery of non-fermentable fractions (e.g. lignin). Out of the many available lignocellulosic feedstocks some have been considered to be less tractable because the pretreatment required to make them usable includes acid hydrolysis or steam explosion with an acid catalyst. These pretreatments may lead to negative impacts on downstream processing and may lower ethanol yield or lower the value of the recoverable by-products. Also, the acidic reactants may cause corrosion and require expensive materials. Another technology for producing bioethanol from woody materials is the gasification of biomass, followed by fermentation to ethanol using anaerobic bacteria. This eliminates the need for hydrolysis to break up the cellulose and hemicellulose fractions of the biomass. In this process, the lignin fraction can also be converted into ethanol. The choice of conversion method is based on the properties of feedstock. This study will categorize and compare the lignocellulosic feedstock options for lignocellulosic bioethanol plant. Top Keywords Biomass, Lignocellulosic materials, Bioethanol, Biofuels. Top | Introduction Biofuels are a potential candidate for enhancing the energy security of countries that are currently dependent on petroleum imports. The most abundant bioenergy feedstocks are lignocellulosic materials. Bioethanol is one of the biofuels that can be produced from lignocellulosic feedstocks and can be blended with gasoline. The lignocellulosic materials can be grouped into three main categories; agricultural, forestry and recycled materials. Agricultural and forestry materials includes material left in fields after the crop has been harvested, such as corn stover, wheat stalks and bagasse from sugar cane, dedicated energy crops such as switch grass, and trees. Recycled materials include waste office paper, newspapers and other mixed papers. Collectively, they are called lignocellulosic biomass and consist of two basic constituents: carbohydrate polymers (called cellulose and hemicelluloses) that can be converted to sugars, and a non-fermentable fraction called lignin that can be burned for production of electricity and/or heat. The key steps in lignocellulosic bioethanol production are pretreatment, enzymatic hydrolysis, fermentation and recovery of the non-fermentable fraction (e.g. lignin). |
Of the various available lignocellulosic feedstocks some have been considered to be less tractable because the pretreatment required to make them usable includes acid hydrolysis or steam explosion with an acid catalyst. These pretreatments may lead to negative impacts on downstream processing and may lower ethanol yield or lower the value of recoverable by-products. Also, the acidic reactants may cause corrosion and require expensive materials for the processing equipment. Another technology for producing bioethanol from woody materials is gasification, followed by fermentation to ethanol using anaerobic bacteria. This eliminates the need for hydrolysis to break up the cellulose and hemicellulose fractions of the biomass. In this process, the lignin fraction can also be converted into ethanol. The choice of best conversion method is based on the properties of the feedstock. The presence of more sugars and starch makes a feedstock much desirable for ethanol production because sugars and starch are much easier to convert to ethanol than cellulose and hemicellulose. Fibrous materials may contain more cellulose, hemicellulose, lignin and lesser sugars than non-fibrous materials. Furthermore, the amount of lignin, moisture, ash and silica also affects the conversion process. |
Ethanol industry is primarily based on relatively expensive starch feedstocks such as corn, although some potato processing residuals are also used. Integration of new lignocellulosic feedstocks that are regionally available into these facilities has not been demonstrated at a sufficiently meaningful scale to evaluate the technical and cost implications. This study will categorize and compare lignocellulosic feedstock options for a bioethanol plant. If successful, this work will enable the utilization of lignocellulosic feedstocks for the production of fuel-ethanol, and will lower the production cost of ethanol. |
Top Feedstock Conversion of biomass to ethanol is based on the chemical properties of the feedstock. For example, fibrous materials may contain more cellulose, hemicellulose, lignin and less sugars, than non-fibrous materials. The presence of more sugars and starch makes a feedstock more desirable for ethanol production, because sugars and starch are easier to convert to ethanol than cellulose and hemicellulose. Furthermore, the amount of lignin, moisture, ash and silica also affects the conversion process. Table 1 shows the composition of various biomass feedstocks and table 2 shows the ultimate and proximate analysis of biomass feedstocks. |
Table 3 shows estimates of the operating cost to produce alternate fuels taken from Wright and Brown [1]. The figure for the operating cost of a grain ethanol plant and for a cellulosic ethanol plant can be considered to reflect the relative difficulty of conversion of cellulosic material to ethanol compared with grain-based ethanol. For grain ethanol and cellulosic ethanol, these operating cost estimates convert to $170/metric ton and $245/metric ton, respectively. |
The quantity of ethanol is based on the composition of the feedstock. For example, some materials may contain more cellulose, hemicellulose, and less lignin and other materials. Since the lignin cannot be converted to sugars and fermented to ethanol it reduces the yield of ethanol per ton of biomass. Table 1 shows the theoretical ethanol yield of various feedstocks. The amount of fermentable sugars in a lignocellulosic material is one of the important parameter in selecting feedstock for lignocellulosic ethanol production. Therefore the percentage of lignin and sugar content in feedstock determine the best feedstock for ethanol production. Experiments were done on regionally available feedstocks kenaf, douglas fir and black locust. The sugar and lignin content were determined to demonstrate their potential of as feedstock for bioethanol plant. |
Top Materials and Methods Among the various available woody biomass feedstocks Kenaf, Douglas Fir and Black Locust samples were used. The Kenaf samples were given by Pacific Northwest National Laboratory, Richland, WA. The lignin and sugar content were compared. The samples were milled and were classified to pass a 0.5 mm-mesh screen. |
Determination of Lignin and Sugar Content The known amount of kenaf sample was taken in sintered thimble. The sintered thimble was plugged with cotton wool and was placed in the soxhlet apparatus. 150 mL dichloromethane was added to the boiling flask with some boiling stones. The extraction device was connected and the condenser was turned on. The solvent was heated to reflux. The condenser cooled the solvent vapor and was separated from the extract. The extract was transferred from boiling flasks to pre-weighed round bottom flask. The extract was evaporated to constant weight in a rotary evaporator. The dichloromethane was separated from the extract by evaporating it in round bottom flasks and subsequently cooled by running water into another different container. 200 mg of extracted sample was taken into a small test tube and sulfuric acid (about 2ml, 72%) was added to sample and incubate for 60 mins at 30°C with regular stirring using glass rod. The primary hydrolyzate was transferred into 200 mL Erlenmeyer flask with the aid of distilled water. The flask was covered with a small beaker and was placed in a pressure cooker. It was heated until started to hiss. (secondary hydrolysis step). After cooling the secondary hydrolyzate was filtered through the crucibles and washed with 40 ml of distilled water. Filterate was transferred to 250 ml volumetric flask. The remaining in the crucible is Kalson Lignin and was oven dried over night at 104°C. Kalson lignin content was calculated based on oven dry original wood basis and extractive free wood basis. The volumetric flask containing secondary hydrolysis filterate was allowed to reach room temperature. 5 ml of filterate was taken using pipette and inositol was added as an internal standard. Small amount of lead carbonate was added to make the solution neutral. It was centrifuged for 5 mins and was transferred to a plastic syringe. The solution was then passed through a small ion exchange cartridge. The filterate was collected into a HPLC vial. HPLC analysis A 100 ml standard solution containing known amount of glucose, mannose, galactose, xylose, arbinose and inositol was prepared. The samples and standards into were placed in HPLC autosampler. HPLC is the Waters Breeze system, the columns were two Phenomenex columns for carbohydrates operated at 90°C with a flow of 0.5 ml/min. Injection volume was 20 μl. The detector used was a refractive index detector for the non chronophoric sugars. Data analysis was done using Breeze software package. The calibration plot was plotted and the amount of sugar was calculated using the formula. The amount of sugars was calculated on anhydro sugar basis and hydrolysis loss factor was used in calculations. Top Results The average lignin content of Kenaf1, Kenaf2, Douglas fir and Black locust is 10.96%, 8.99%, 20.49% and 20.89% respectively, and average total sugar content is 59.64%, 80.43%, 56.54% and 55.68% respectively. Table 4 shows the determined values for lignin and sugar content of the various samples. Figure 1 is the bar chart showing the comparison of the experimental results. The difference in lignin content of Kenaf1 and Kenaf2 is due to difference in working conditions and environment parameters. |
Top Discussion and Conclusion The percentage of sugar content in Kenaf is more and lignin content is less than other species (refer Table 4). As ethanol yield is directly related to amount of sugars in the feedstock and inversely related to amount of lignin. Therefore we may say that among selected samples, Kenaf is a better lignocellulosic feedstock for ethanol production. The next step is to produce ethanol by fermentation of the produced sugars and compare ethanol yield. The experimental yield will be compared with the theoretical yield (Table 1). |
Top Figure Figure 1:: Comparison average lignin content and average sugar content of Kenaf1, Kenaf2, Douglas Fir and Black Locust
| 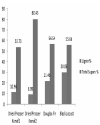 | |
|
Tables Table 1:: The composition of various fibers
| Type of Fiber | Compound | %by weight of total | Theoretical Ethanol Yield (gallons/ton) [2] | | | Cellulose | Lignin | Pentosan | Ash | Silica | Stalk Fiber | Rice | 28–48 | 13–16 | 23–28 | 15–20 | 9—14 | 89–132 | | Wheat | 29–51 | 16–21 | 26–32 | 4.5–9 | 3—7 | 96.1–144.3 | | Barley | 31–45 | 14–15 | 24–29 | 5—7 | 3—6 | 128 | | Oat | 31–48 | 16–19 | 27–38 | 6—8 | 4–6.5 | 101.3–150 | | Rye | 33–50 | 16–19 | 27–30 | 2—5 | 0.5–4 | 104.7–139 | Cane Fiber | Bagasse | 32–48 | 19–24 | 27–32 | 1.5–5 | 0.7–3.5 | 103–139.2 | | Bamboo | 26–43 | 21–31 | 15–26 | 1.7–5 | 0.7 | 71.2–119.9 | Grass Fiber | Esparto | 33–38 | 17–19 | 27–32 | 6—8 | – | 104.7–122.2 | | Sabai | – | 22 | 24 | 6 | – | 43.2 | Reed Fiber | Phragmites communis | 44–46 | 22–24 | 20 | 3 | 2 | 110.8–114.2 | Bast fiber | Seed Flax | 43–47 | 21–23 | 24–26 | 5 | – | 116.3–126.7 | | Kenaf | 44–57 | 15–19 | 22–23 | 2—5 | – | 114.4–138.3 | | Jute | 45–63 | 21–23 | 18–21 | 0.5–2 | – | 108.9–144.9 | | Hemp | 57–77 | 9 – 13 | 14–17 | 0.8 | – | 122.1–161.5 | | Ramie | 87–91 | – | 5—8 | – | – | 156.9–169.1 | Core Fiber | Kenaf | 37–49 | 15–21 | 18–24 | 2—4 | – | 95.3–126.5 | | Jute | 41–48 | 21–24 | 18–22 | 0.8 | – | 102.1–121.2 | Leaf Fiber | Abaca (Manila) | 56–63 | 7 – 9 | 15–17 | 3 | – | 122.2–137.7 | | Sisal (agave) | 47–62 | 7 – 9 | 21–24 | 0.6–1 | – | 117.7–148.6 | Seed Hull Fiber | Cotton | 85–90 | 0.7 - 1.6 | 1—3 | 0.8–2 | – | 146.3–158.4 | Wood Fiber | Coniferous | 40–45 | 26–34 | 7—14 | <1 | – | 80.6–101.7 | | Deciduous | 38–49 | 23–30 | 19–26 | <1 | – | 98.8–130.1 |
| | Table 2:: Biomass Feedstocks: Ultimate and Proximate analysis [3-5]
| | Ultimate Analysis (wt% dry basis) | Proximate Analysis (wt% dry basis) | | C | H | N | O | S | Ash | Moisture | Volatiles | Fixed Carbon | Heating Value (MJ/kg) | Agricultural Residues | Sawdust | 50 | 6.3 | 0.8 | 43 | 0.03 | 0.03 | 7.8 | 74 | 25.5 | 19.3 | Bagasse | 48 | 6.0 | | 42 | | 4 | 1 | 80 | 15 | 17 | Corn Cob | 49 | 5.4 | 0.4 | 44.6 | | 1 | 5.8 | 76.5 | 15 | 17 | Short Rotation Woody Crops | Beech Wood | 50.4 | 7.2 | 0.3 | 41 | 0 | 1.0 | 19 | 85 | 14 | 18.4 | Herbaceous Energy Crops | Switchgrass | 43 | 5.6 | 0.5 | 46 | 0.1 | 4.5 | 8.4 | 73 | 13.5 | 15.4 | Straw | 43.5 | 4.2 | 0.6 | 40.3 | 0.2 | 10.1 | 7.6 | 68.8 | 13.5 | 17 | Miscanthus | 49 | 4.6 | 0.4 | 46 | 0.1 | 1.9 | 7.9 | 79 | 11.5 | 12 | Muncipal Solid Waste | Dry Sewage | 20.5 | 3.2 | 2.3 | 17.5 | 0.6 | 56 | 4.7 | 41.6 | 2.3 | 8 | Coals | Subbituminous | 67.8 | 4.7 | 0.9 | 17.2 | 0.6 | 8.7 | 31.0 | 43.6 | 47.7 | 24.6 | Bituminous | 61.5 | 4.2 | 1.2 | 6.0 | 5.1 | 21.9 | 8.7 | 36.1 | 42.0 | 27.0 |
| | Table 3:: Operating costs of biofuels ($/gasoline gallon equivalent)
| Fuel | $/gallon (gasoline equivalent) | Grain Ethanol | 1.22 | Cellulosic Ethanol | 1.76 | Methanol | 1.28 | Hydrogen | 1.05 | Fisher-Tropsch | 1.8 |
| | Table 4:: Comparison of lignin content and sugar content of Kenaf, Dried Prosser Kenaf, Douglas Fir and Black Locust
| Property#↓ | Spices → | | Dried Prosser Kenaf1 | Dried Prosser Kenaf2 | Douglas Fir | Black Locust | Lignin Content (%) | L1 | | 13.55 | 8.79 | 20.49 | 29.89 | | L2 | | 8.36 | 7.88 | 22.42 | 30.22 | | L(ave) | | 10.96 | 8.99 | 21.46 | 30.06 | Sugar Content (%) | Glucose | S1 | 34.05 | 45.00 | 42.35 | 36.66 | | | S2 | 36.09 | 48.03 | 26.50 | 26.87 | | Xylose | S1 | 10.78 | 13.08 | 6.53 | 19.46 | | | S2 | 13.15 | 15.71 | 5.25 | 15.41 | | Galactose | S1 | 2.99 | 0 | 6.96 | 3.04 | | | S2 | 4.35 | 8.22 | 5.52 | 3.55 | | Arabinose | S1 | 2.87 | 0 | 2.82 | 0 | | | S2 | 4.28 | 5.72 | 2.33 | 2.32 | | Mannose | S1 | 2.88 | 0 | 8.85 | 2.46 | | | S2 | 2.03 | 3.46 | 5.96 | 1.58 | Total Sugar content % | | S(ave) | 59.64 | 80.43 | 56.54 | 55.68 |
|
| |
| Acknowledgement The authors would like to acknowledge Noridah Osman (Department of Forest Product, University of Idaho) for help during the experiments and Idaho National Laboratory for providing funds to conduct this research project. Top | |
|
|
|