|
|
|
Supercritical Biodiesel Production from Raw Soybean Oil Quesada Joaquín1,*, Olivares Pilar1 1Department of Chemical Engineering, Faculty of Chemistry, University of Murcia, Spain *Email ID: quesamed@um.es
Abstract This paper describes the supercritical methanol transesterification of raw soybean oil for biodiesel production in a batch stirred tank reactor without catalyst and looks at the main variables affecting the yield of biodiesel: the methanol-to-oil molar ratio and reaction temperature. Experiments were carried out for 20 min in the temperature range 250–350°C at methanol-to-oil molar ratios of between 20:1 and 53:1. The reactions were monitored by gel permeation chromatography (GPC) to determine the content of monoglycerides, diglycerides and triglycerides, and by gas chromatography (GC/FID) to analyse the individual methyl esters and to calculate the yield of biodiesel. The reaction conditions that led to good yields of biodiesel (72%) were a temperature of 350°C and a methanol-to-oil molar ratio of 45. There was no undesirable thermal decomposition of the fatty acid chains in these conditions. Due to the risk of thermal cracking above 350°C, reaction times need to be lengthened to complete the transesterification of monoglycerides and diglycerides remaining in the medium and so provide greater yields of biodiesel. Top Keywords Biodiesel, Supercritical methanol, Soybean oil, Transesterification conditions. Top | Introduction Biodiesel has emerged as an alternative fuel and gained wide acceptance because of some advantages it has over petroleum derived diesel: lower environmental impact [1], higher lubricity, higher cetane number and lower flash point. Biodiesel is made from the triglycerides that exist in biomass, such as animal fats, plant oils (e.g., corn, palm, rapeseed and soybean oils) and algae. Waste cooking oils and animal fats are especially attractive feedstocks because they are inexpensive and provide a waste-to-energy opportunity. |
Biodiesel can be produced by catalyzed or uncatalyzed transesterification. The former process is currently used in commercial biodiesel production, while the latter method, which typically involves supercritical conditions, was developed to facilitate processing of lower quality, and hence lower cost, feedstocks. However, biodiesel synthesis using supercritical methanol has a drawback: the high cost of the necessary apparatus which uses high temperature and pressure, and which are therefore unsuitable for large scale industrial production. This has led to many researchers to look for ways to decrease the severity of the reaction conditions. For example, co-solvents, such as carbon dioxide [2] and propane [3], and heterogeneous catalysts, such as calcium oxide [4], added into the reaction mixture can decrease the operating temperature, the working pressure and the amount of alcohol. In the supercritical method, the acid value and water content do not have a negative effect on the reaction, and may even provide an impetus to the reaction under certain conditions [5]. Furthermore, purification of the reaction products is simpler than in the catalyzed process and non-polluting effluents are generated. |
In the research described, biodiesel production from raw soybean oil with supercritical methanol in a batch stirred tank reactor was investigated without the use of catalysts. Experiments were carried out for 20 min, and the influence of the reaction temperature (250–350°C) and the methanol-to-oil molar ratio (20:1–53:1) was studied. In the near future, once the optimal reaction conditions have been established, a study using heterogeneous catalysts (prepared jointly by the University of the Basque Country and the Public University of Navarra, Spain) will be carried out in a search for milder reaction conditions, which will lower production costs even more. |
Top Experimental Setup The reaction was carried out for 20 min in a batch stirred tank reactor (a stainless steel cylindrical autoclave of 83 ml capacity) to investigate the influence of the reaction temperature (250–350°C) and the methanol-to-oil molar ratio (20:1–53:1). The reactor was introduced pneumatically by a mechanical arm into a smelted salt bath which permits the reaction mixture to reach the desired temperature in less than 9 min. In all the experiments, the reaction time started when the reactor was immersed in the salt bath. The reactor was continuously shaken orbitally (70 rpm), and, after removal from the salt bath, introduced in a water bath to stop the reaction. The product obtained was evaporated in rotavapor to remove the methanol and stored in refrigerator before analysis. |
The reaction was monitored by gel permeation chromatography (GPC) to determine the content of monoglycerides, diglycerides and triglycerides, and by gas chromatography (GC/FID) to analyse the individual methyl esters and to calculate the yield of biodiesel according to the UNE-EN 14103:2003 norm. Two apparatus used were: (1) a LC-Module I Waters liquid cromatograph coupled to a 2414 Waters refractive index detector and fitted with two Styragel GPC columns (HR0.5 and HR1, 7.8 x 300 mm and 5 ìm particle size) connected in series. The analysis were carried out in isochratic conditions using tetrahydrofuran as eluent at 0.9 ml/min; (2) a 3900 Varian gas chromatograph equipped with a CP 8400 Varian autosampler, coupled to a FID detector and fitted with a CP-Wax 52-CB capillary column (30 m x 0.32 mm, 0.25 ìm film). Helium was used as carrier gas at a flow rate of 1 ml/min with a split ratio of 1:50. The oven temperature was always 210°C. The injector and detector temperature was 250°C. |
Top Results and Discussion The main results obtained during the transesterification of soybean oil with supercritical methanol are shown in Tables 1 and 2, where the influence of the methanol-to-oil molar ratio and temperature on the reaction can be observed. The yield of biodiesel was calculated in two ways: (1) taking into account all the methyl esters (peaks) detected in the GC chromatogram (total biodiesel), and (2) taking into account only the identified methyl esters (known biodiesel); in both cases, the yield was calculated as a percentage of the quantity of methyl esters that can theoretically be obtained from the fatty acid composition of the oil. |
To avoid any influence of the methanol-to-oil molar ratio on the working pressure, we initially studied the influence of the volume of methanol used to fill the reactor (84 ml capacity) on the pressure reached inside the reactor at different temperatures (see Figure 1). As expected, it was observed that, regardless of the filling volume of the reactor, the higher the temperature, the greater the pressure inside the reactor. Moreover, the higher the filling volume of the reactor, the greater the dependence between temperature and pressure. The introduction of volumes above 60 ml of methanol led to excessively high pressures, even at the lowest temperature tested (250°C), which could endanger the safe operation of the reactor. With a filling volume of 60 ml, a pressure of 225 bar was reached at 250°C, whereas at 350°C the pressure was 400 bar. Because this pressure range (225–400 bar) is the most commonly studied by authors [6, 7], a filling volume of 60 ml was chosen for all the experiments. On the other hand, when the reactor was filled only with oil, the amount introduced does not cause a significant increase in pressure, and values lower than 20 bar are reached, regardless of the temperature applied. As shown in Figure 2, with a filling volume of 60 ml (methanol + oil), the pressure reached inside the reactor for different temperatures and methanol-to-oil molar ratios was little influenced by the molar ratio, whatever the temperatura applied, the only exception being the 20.2 molar ratio. |
The conversion of oil and the yield of biodiesel, monoglycerides and diglycerides were studied during reaction. The conversion of oil and the yield of biodiesel, both total and known, as a function of reaction temperature are represented in Figures 3, 4 and 5, respectively, for different methanol-to-oil molar ratios. The differences between the yield of total and known biodiesel are quite small, indicating that practically all the methyl esters detected were identified and that, therefore, no methyl esters other than those indicated in the method were generated. It was observed that both the conversion of oil and the yield of biodiesel increased with temperature, a conversion close to 100% at 350°C being reached, regardless of the methanol-to-oil molar ratio used, with the exception of the molar ratio of 20.2, which led to a conversion of around 70%. At the same temperature (350°C) we obtained the highest yield of total biodiesel (close to 70% for molar ratios above 30), which was significantly lower than the conversion of oil. The fact that the yield of biodiesel was always lower than the conversion of oil at all temperatures indicates that part of the triglycerides were not converted to methyl esters, but probably to intermediate products such as monoglycerides and diglycerides. It was also noted that both the conversion of oil and the yield of biodiesel increased slightly with the methanol-to-oil molar ratio, whatever the temperature. The pressure remaining in the reactor after the reaction was always atmospheric, suggesting the absence of thermal cracking reactions of the fatty acid chains, which would normally lead to the formation of methane and carbon dioxide. Since temperatures above 350°C may cause these undesirable reactions, it is not recommended to work at temperatures above 400°C [7]. Therefore, it can be concluded that the best reaction conditions to carry out the transesterification of soybean oil with supercritical methanol were a temperature of 350°C for 20 min and a methanol-to-oil molar ratio of 45.8. These results are consistent with those obtained by several authors [7-11] who indicated an optimal temperature within the range 300–350°C and a molar ratio of 40–45. |
The yield of monoglycerides (see Figure 6) passed through a maximum at about 325°C for all the methanol-to-oil molar ratios studied. This maximum (between 105 and 132 mg/g of initial triglycerides) increases with the molar ratio applied. As shown in Figure 7, the behavior of diglycerides was similar, reaching a maximum of 267 mg/g of initial triglycerides at about 300°C for a methanol-to-oil molar ratio of 53.3; in this case, the maximum was little influenced by the molar ratio. The trends observed suggest that diglycerides would disappear at about 360°C, whereas the yield of monoglycerides would become zero at about 400°C. The disappearance of monoglycerides and diglycerides would lead to higher yields of biodiesel, which would be close to 100% if there were no thermal decomposition reactions of the fatty acid chains. |
As shown in table 2, the individual yield of the main methyl esters obtained increases with reaction temperature and only slightly with the methanol-to-oil molar ratio, although this increase was very small for molar ratios above 30. As expected, the highest yields obtained were those of methyl palmitate, methyl oleate and methyl linoleate because soybean oil has a high content of these kinds of fatty acid chain. |
According to some authors [7, 12], thermal decomposition and dehydrogenation (undesirable reactions) of unsaturated fatty acid chains (particularly those of linoleic and linolenic acid type) occurs at temperatures between 300 and 350°C, with a consequent loss of biodiesel yield. In our study, the yield of the main unsaturated fatty acid methyl esters (methyl oleate, methyl linoleate and methyl linolenate) did not decrease in the temperature range tested (250–350°C) (see Table 2), indicating that undesirable decomposition reactions of fatty acid chains were not produced in the experimental conditions applied. |
To clearly observe the influence of the methanol-to-oil molar ratio on the conversion of oil and the yield of total biodiesel, Figures 8 and 9 represent these two responses versus the molar ratio for temperatures of 250, 275, 300, 325 and 350°C. As can be seen, both the conversion of oil and the yield of biodiesel increase with the molar ratio up to molar ratios of 40–45, above which these two responses leveled off for all temperatures tested, the only exception being at 250°C, at which the responses remained practically constant over the entire range of molar ratios tested. These results agree with those obtained by other authors [7–11], who obtained optimum molar ratios in the range 40–45, depending on the type of oil used and the reaction temperature applied. |
Table 3 shows the mass balance in the reactor. The balance was made taking into account that in each experiment, the sum of the amount of triglycerides converted and the theoretical amount of methanol reacted (calculated from the amount of methyl esters generated) must be equal to the sum of the generated amounts of methyl esters, monoglycerides and diglycerides plus the theoretical amount of glycerol generated. As can be seen, the results indicate that the mass balance in the reactor was correctly accomplished (error lower than 5% in most cases, and not exceeding 16% in any case), indicating that no undesirable side or thermal decomposition reactions were produced. |
Top Conclusions Based on the results obtained, it can be concluded that the transesterification conditions of soybean oil with supercritical methanol that lead to good yields of biodiesel (72%), without producing undesirable thermal cracking reactions of fatty acid chains, are a temperature of 350°C applied for 20 min and a methanol-to-oil molar ratio of 45. Because the application of temperatures above 350°C can lead to the thermal decomposition of fatty acid chains, greater yields of biodiesel could be achieved by applying longer reaction times to complete the transesterification of monoglycerides and diglycerides remaining in the medium. |
Top Figures Figure 1.: Pressure generated in the reactor as a function of temperature for filling volumes of methanol of: ♦, 30 ml; ∎, 40 ml;, 50 ml; ♦, 60 ml; ⚫, 70 ml.
| 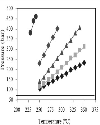 | |
| Figure 2.: Pressure generated in the reactor as a function of reaction temperature for methanol-to-oil molar ratios of: ♦, 20.2; ∎, 30.2; ▲, 37; ♦, 45.8; ⚫, 53.3 (filling volume of the reactor = 60 ml, reaction time = 20 min).
| 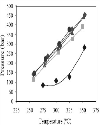 | |
| Figure 3.: Conversion of oil as a function of reaction temperature for methanol-to-oil molar ratios of: ♦, 20.2; ∎, 30.2; ▲, 37; ♦, 45.8; ⚫, 53.3 (reaction time = 20 min).
| 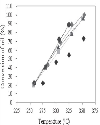 | |
| Figure 4.: Yield of total biodiesel as a function of reaction temperature for methanol-to-oil molar ratios of: ♦, 20.2; ∎, 30.2; ▲, 37; ♦, 45.8; ⚫, 53.3 (reaction time = 20 min).
| 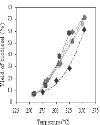 | |
| Figure 5.: Yield of known biodiesel as a function of reaction temperature for methanol-to-oil molar ratios of: ♦, 20.2; ∎, 30.2; ▲, 37; ♦, 45.8; ⚫, 53.3 (reaction time = 20 min).
| 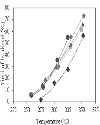 | |
| Figure 6.: Yield of monoglycerides as a function of reaction temperature for methanol-to-oil molar ratios of: 20.2; ∎, 30.2; ▲, 37; ♦, 45.8; ⚫, 53.3 (reaction time = 20 min).
| 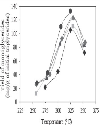 | |
| Figure 7.: Yield of diglycerides as a function of reaction temperature for methanol-to-oil molar ratios of: ♦, 20.2; ∎, 30.2; ▲. 37; ♦, 45.8; ⚫, 53.3 (reaction time = 20 min).
|  | |
| Figure 8.: Conversion of oil as a function of methanol-to-oil molar ratio for reaction temperatures of: ♦, 250°C; ∎, 275°C; ▲, 300°C; ♦, 325°C; ⚫, 350°C (reaction time = 20 min).
| 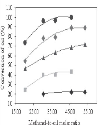 | |
| Figure 9.: Yield of total biodiesel as a function of methanol-to-oil molar ratio for reaction temperatures of: ♦, 250°C; ∎, 275°C; ▲, 300°C; ♦, 325°C; ⚫, 350°C (reaction time = 20 min).
| 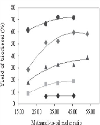 | |
|
Tables Table 1:: Conversion of the oil and yield of monoglycerides, diglycerides and biodiesel during transesterification of soybean oil with supercritical methanol.
| M/O | T (°C) | P (bar) | CO (%) | YD* | YM* | YTB (%) | YKB (%) | 20.20 | 275 | 83 | 24.00 | 130.30 | 21.72 | 8.51 | 1.57 | 20.20 | 300 | 107 | 45.99 | 239.75 | 45.18 | 18.11 | 16.17 | 20.20 | 325 | 128 | 54.30 | 168.08 | 105.16 | 28.66 | 27.36 | 20.20 | 353 | 283 | 73.23 | 48.34 | 72.48 | 61.27 | 56.10 | 30.20 | 257 | 112 | 20.01 | 115.32 | 12.51 | 6.58 | 5.53 | 30.20 | 280 | 200 | 40.03 | 193.72 | 41.90 | 16.19 | 14.01 | 30.20 | 305 | 256 | 57.47 | 254.12 | 84.65 | 30.77 | 28.47 | 30.20 | 330 | 325 | 78.17 | 126.74 | 110.95 | 51.00 | 46.50 | 30.20 | 350 | 390 | 95.90 | 45.42 | 82.27 | 66.32 | 61.37 | 37.00 | 278 | 192 | 40.05 | 191.90 | 36.16 | 17.03 | 14.96 | 37.00 | 304 | 280 | 63.23 | 267.03 | 86.41 | 32.93 | 30.41 | 37.00 | 330 | 360 | 79.00 | 167.46 | 124.09 | 52.27 | 48.84 | 37.00 | 352 | 445 | 96.47 | 43.55 | 83.85 | 71.95 | 66.34 | 45.80 | 257 | 141 | 22.20 | 128.47 | 25.66 | 6.92 | 6.07 | 45.80 | 284 | 235 | 43.04 | 189.79 | 41.16 | 18.81 | 18.18 | 45.80 | 308 | 290 | 68.47 | 246.56 | 93.06 | 32.58 | 30.06 | 45.80 | 330 | 377 | 88.89 | 148.99 | 123.77 | 59.30 | 54.94 | 45.80 | 354 | 454 | 100.00 | 48.16 | 87.43 | 71.49 | 73.43 | 53.30 | 259 | 145 | 22.02 | 128.20 | 27.87 | 6.76 | 5.20 | 53.30 | 280 | 220 | 40.03 | 201.17 | 42.51 | 13.76 | 11.93 | 53.30 | 306 | 298 | 71.60 | 266.80 | 110.41 | 38.55 | 35.42 | 53.30 | 325 | 374 | 88.76 | 183.08 | 132.74 | 58.23 | 54.47 |
|
| | Table 2:: Yield of the individual methyl esters obtained during transesterification of soybean oil with supercritical methanol (mg/g of initial triglycerides).
| M/O | T (°C) | RC 14:0 | RC 16:0 | RC 16:1 | RC 18:0 | RC 18:1 | RC 18:2 | RC 18:3 | RC 20:0 | RC 20:1 | 20.20 | 275 | 0.00 | 9.34 | 0.00 | 2.25 | 4.08 | 0.00 | 0.00 | 0.00 | 0.00 | 20.20 | 300 | 0.00 | 21.36 | 0.00 | 7.16 | 39.38 | 91.02 | 2.75 | 0.00 | 0.00 | 20.20 | 325 | 0.20 | 34.29 | 0.00 | 12.02 | 63.26 | 144.83 | 17.12 | 0.63 | 0.12 | 20.20 | 353 | 0.43 | 78.39 | 0.92 | 32.74 | 163.76 | 273.86 | 5.63 | 2.63 | 1.43 | 30.20 | 257 | 0.00 | 7.69 | 0.00 | 2.43 | 12.95 | 29.70 | 2.53 | 0.00 | 0.00 | 30.20 | 280 | 0.00 | 18.41 | 0.00 | 6.32 | 33.80 | 79.55 | 1.99 | 0.00 | 0.00 | 30.20 | 305 | 0.22 | 37.64 | 0.30 | 13.40 | 68.84 | 157.12 | 5.93 | 0.61 | 0.61 | 30.20 | 330 | 0.36 | 68.51 | 0.00 | 21.80 | 127.44 | 239.90 | 6.98 | 0.00 | 0.00 | 30.20 | 350 | 0.46 | 93.53 | 0.00 | 30.93 | 180.96 | 290.12 | 17.69 | 0.00 | 0.00 | 37.00 | 278 | 0.00 | 20.36 | 0.00 | 6.31 | 35.97 | 84.72 | 2.23 | 0.00 | 0.00 | 37.00 | 304 | 0.23 | 40.19 | 0.00 | 14.37 | 72.09 | 170.17 | 7.04 | 0.00 | 0.00 | 37.00 | 330 | 0.37 | 63.79 | 0.00 | 22.65 | 119.49 | 267.94 | 14.20 | 0.00 | 0.00 | 37.00 | 352 | 0.57 | 96.44 | 1.08 | 34.21 | 180.66 | 334.37 | 9.13 | 2.88 | 2.73 | 45.80 | 257 | 0.00 | 8.59 | 0.00 | 2.48 | 14.35 | 35.26 | 0.00 | 0.00 | 0.00 | 45.80 | 284 | 0.00 | 23.37 | 0.00 | 7.44 | 42.90 | 100.71 | 7.35 | 0.00 | 0.00 | 45.80 | 308 | 0.26 | 40.48 | 0.00 | 13.37 | 71.26 | 168.85 | 6.41 | 0.00 | 0.00 | 45.80 | 330 | 0.41 | 66.63 | 0.00 | 26.30 | 138.30 | 301.24 | 11.08 | 1.90 | 1.30 | 45.80 | 354 | 0.57 | 105.10 | 0.00 | 34.34 | 200.13 | 376.85 | 17.28 | 0.00 | 0.00 | 53.30 | 259 | 0.00 | 7.25 | 0.00 | 0.82 | 13.07 | 30.85 | 0.00 | 0.00 | 0.00 | 53.30 | 280 | 0.00 | 14.87 | 0.00 | 3.96 | 29.12 | 70.17 | 1.17 | 0.00 | 0.00 | 53.30 | 306 | 0.31 | 47.01 | 0.00 | 15.05 | 85.86 | 198.48 | 7.51 | 0.00 | 0.00 | 53.30 | 325 | 0.47 | 69.50 | 0.00 | 22.51 | 132.32 | 300.75 | 18.96 | 0.12 | 0.11 |
|
| | Table 3:: Mass balance in the reactor for supercritical methanol transesterification of soybean oil.
| M/O | T (°C) | ME* | MG* | DG* | TG* | Gly* | MeOH* | TG+ MeOH* | ME+MG+DG+ Gly* | Error (%) | 20.2 | 275 | 85.0 | 21.7 | 130.3 | 241.0 | 25.3 | 26.4 | 267.4 | 262.3 | 1.9 | 20.2 | 300 | 180.9 | 45.2 | 239.7 | 452.0 | 47.4 | 49.5 | 501.5 | 513.2 | -2.3 | 20.2 | 325 | 286.2 | 105.2 | 168.1 | 543.0 | 57.0 | 59.4 | 602.5 | 616.4 | -2.3 | 20.2 | 353 | 612.0 | 72.5 | 48.3 | 732.3 | 76.8 | 80.2 | 812.5 | 809.6 | 0.4 | 30.2 | 257 | 65.7 | 12.5 | 115.3 | 198.0 | 20.8 | 21.7 | 219.7 | 214.3 | 2.5 | 30.2 | 280 | 161.7 | 41.9 | 193.7 | 402.0 | 42.2 | 44.0 | 446.0 | 439.4 | 1.5 | 30.2 | 305 | 307.3 | 84.7 | 254.1 | 574.7 | 60.3 | 62.9 | 637.6 | 706.4 | -10.8 | 30.2 | 330 | 509.3 | 110.9 | 126.7 | 781.7 | 82.0 | 85.6 | 867.3 | 829.0 | 4.4 | 30.2 | 350 | 662.4 | 82.3 | 45.4 | 959.0 | 100.6 | 105.0 | 1064.0 | 890.7 | 16.3 | 37.0 | 278 | 170.1 | 36.2 | 191.9 | 405.0 | 42.5 | 44.3 | 449.3 | 440.6 | 1.9 | 37.0 | 304 | 328.9 | 86.4 | 267.0 | 632.3 | 66.3 | 69.2 | 701.5 | 748.7 | -6.7 | 37.0 | 330 | 522.0 | 124.1 | 167.5 | 790.0 | 82.9 | 86.5 | 876.5 | 896.4 | -2.3 | 37.0 | 352 | 718.6 | 83.8 | 43.6 | 964.7 | 101.2 | 105.6 | 1070.3 | 947.2 | 11.5 | 45.8 | 257 | 69.1 | 25.7 | 128.5 | 221.0 | 23.2 | 24.2 | 245.2 | 246.4 | -0.5 | 45.8 | 284 | 187.9 | 41.2 | 189.8 | 430.0 | 45.1 | 47.1 | 477.1 | 463.9 | 2.8 | 45.8 | 308 | 325.4 | 93.1 | 246.6 | 684.7 | 71.8 | 75.0 | 759.7 | 736.9 | 3.0 | 45.8 | 330 | 592.3 | 123.8 | 149.0 | 888.9 | 93.2 | 97.3 | 986.2 | 958.3 | 2.8 | 45.8 | 354 | 714.0 | 87.4 | 48.2 | 1000.0 | 104.9 | 109.5 | 1109.5 | 954.5 | 14.0 | 53.3 | 259 | 67.6 | 27.9 | 128.2 | 222.0 | 23.3 | 24.3 | 246.3 | 246.9 | -0.2 | 53.3 | 280 | 137.5 | 42.5 | 201.2 | 398.0 | 41.7 | 43.6 | 441.6 | 422.9 | 4.2 | 53.3 | 306 | 385.0 | 110.4 | 266.8 | 716.0 | 75.1 | 78.4 | 794.4 | 837.3 | -5.4 | 53.3 | 325 | 581.6 | 132.7 | 183.1 | 887.6 | 93.1 | 97.2 | 984.8 | 990.5 | -0.6 |
|
| |
| Acknowledgements The authors would like to acknowledge the financial support from the Council of Education, Science and Research of Murcia (Murcia, Spain) in the form of a research project (ref: SUE-TQ 07/01–0006). Top | |
|
|
|