|
|
|
Catalytic Applications of oxalic acid treated CuO/HZSM-5 in Methanol Conversion to Hydrocarbons Zaidi H.A.1,*, Pant K.K.2 1University School of Chemical Technology, Guru Gobind Singh Indraprastha University,Delhi 2Department of Chemical Engineering, Indian Institute of Technology, Hauz Khas, Delhi *Email ID: hasan.azaidi@gmail.com
Abstract A series ofCuO over HZSM-5 catalysts were prepared by wet impregnation technique followed by dealumination using oxalic acid. The loading ofCuO over HZSM-5 was kept between 0 and 9 wt% and treated with oxalic acid. XRD, Surface area analyzer, metal trace analyzer and SEM techniques were used to characterize the catalysts. The higher yield of gasoline range hydrocarbons were obtained with the increase in weight % ofCuO over HZSM-5.Effect of run time on the hydrocarbon yields and methanol conversion was investigated. The activity of the catalyst decreased progressively with time on stream. Relatively lower coke deposition over HZSM-5 catalysts was observed compared to CuO impregnated HZSM-5 catalyst. The effect of run time was studied to investigate the effect oxalic acid treatment on catalyst stability. Top Keywords CuO/HZSM-5, Impregnation, Deactivation, Methanol Conversion. Top Abbreviations OXZ (9): 8.88 wt% CuO/HZSM-5(oxalic acid treated), OXZ(7): 6.89 wt% CuO/HZSM-5(oxalic acid treated), OXZ(5): 4.92 wt% CuO/HZSM-5(oxalic acid treated), OXZ(3): 2.95 wt% CuO/HZSM-5(oxalic acid treated), OZ(0): HZSM-5. Top | Introduction Non-renewable petroleum products presently meet fuel demand of transportation and power generation. However, the increase in demand of petroleum products has lead to hike in the fuel prices. Catalytic conversion of methanol to gasoline and olefins has attracted many researchers due to this reason. Various type of zeolites have been used such as ZSM-5 [1], Ga2O3/HZSM-5 and Ga2O3/WO3 catalysts [2], High silica MFI zeolites impregnated with different metal nitrate of Ag, Ca, Cd, Cu, Ga, In, La and Sr [3] and dealuminated mordenite [4] etc have also been studied. Doping metal oxide into framework usually results in the generation of additional acidic sites, which there by modifies the acidity of the parental material. It facilitates the dehydrating activity of the catalyst and helps to form higher molecular weight hydrocarbons of gasoline range. The deactivation of catalyst in the transformation of methanol to hydrocarbons is mainly due to the coke deposition. |
Top Experimental The starting HZSM-5 was used as a support for CuO. Other starting material such as copper nitrate salt was procured from Merck (Germany). A series of CuO/HZSM-5 catalysts were prepared by impregnation technique by varying the amount of CuO ranging from 0-9wt% doped on the HZSM-5. De-ionized water was used to prepare the solution of weighed copper nitrate. The solution was added to HZSM-5 zeolite pellets. NH4OH solution was added to the slurry of catalyst wetted with the copper nitrate to raise the pH to 5. The final solution was stirred for 12 h at 303 K. The final catalyst slurry was transferred to a rotary evaporator to remove excess water under vacuum at 353 K followed by drying in an oven at 393 K for 12 h. The dried pellets were calcined in a furnace at 823 K for 5 h to decompose Cu complex to CuO. |
It is reported that oxalic acid treated catalysts have better performance for reducing deactivation of catalyst [5]. To investigate the effect of oxalic acid treatment, another batch of the catalyst was prepared by treating 0-9wt% CuO/HZSM-5 catalysts with 1 molar oxalic acid dissolved in de-ionized water for 2 minutes at 353 K. The treated particles were washed thoroughly with de-ionized water and finally dried over night at 393 K in an oven. |
The surface areas and pore volumes of the catalysts were determined by using ASAP 2010 (Micromeritics. USA) by adsorption with nitrogen (99.99% purity) at 77 K, employing the static volumetric technique. |
To determine the actual amount of CuO doped over HZSM-5, and the Si/Al ratio, the catalyst samples were digested with nitric acid at 353 K for 2 h under reflux. The final metal content on the catalyst was determined by a metal trace analyzer (Metrohm 757 VA Computrace, Switzerland). A standard solution of Copper and Zinc nitrates were used for calibration for this purpose. |
To obtain surface textural details of the support, scanning electron microscopy (SEM) of fresh and used samples were done. The morphology and structure of the catalysts were studied using Cambridge 360 scanning electron microscope (SEM). |
Top Results and Discussion The crystal morphology, formation of micropores and property of surface was observed by scanning electron microscopy (SEM). The SEM photographs of various calcined catalysts indicated that there is no significant change in the morphology of the surface structure after doping of CuO and oxalic acid treatment over HZSM-5. Shape of HZSM-5 particle seems to be spherical. Typical SEM photographs of fresh OZ (0), OXZ (7) catalysts are given in Fig. 1 |
Experimental runs were conducted at different temperature to study the effect of temperature on methanol conversion and yield of hydrocarbons over CuO impregnated HZSM-5 catalyst treated with oxalic acid. Fig. 2 shows the product distribution at different temperatures at the same contact time. Methanol conversion and hydrocarbons yield increased with the increase in temperature. There was increase in conversion and liquid hydrocarbons yield upto 673 K, however above 673 K there was no significant improvement in hydrocarbons as shown in Fig. 2. |
At 698 K the catalyst deactivated faster because of rapid coke formation over the surface due to cracking of oligomers into smaller molecules and coke, which deactivates the catalyst. However at medium temperatures oligomerization and cracking are somewhat balanced and cracking is not severe enough to make too much coke; therefore catalyst activity lasts long. Experimental data reveals several interesting qualitative MTG reactions. As shown in the Fig. 2 there was increase in the yield of hydrocarbon with increase in temperature from 635 K to 673 K. It was experimentally observed that 673 K was the optimal temperature for the selective transformation of methanol to hydrocarbons of desirable range. Ethylene and propylene are generally believed to the first olefinic hydrocarbons formed during methanol conversion and they can be easily oligomerized in the temperature range from 635 K to 673 K to produce desirable hydrocarbons of gasoline range. |
As seen from the Fig 2, enhanced yield of aromatics and decreased yield of olefins C2-C3 was observed up to 673 K. As the temperature of the reaction increased, polymerization, cyclization, dehydrogenation and aromatization reactions start and olefins are converted into the higher hydrocarbons. The distributions of aromatics also change strongly with the increasing temperature. The methanol reaction comprised of secondary reaction that converts primary olefins product to gasoline range hydrocarbons. |
The surface area and pore volume of these catalysts were determined by BET method. The results are given in Table 1. The surface area of catalyst decreased on increasing copper oxide loading. Volume of N2 adsorbed decreased with increasing copper oxide content due to partial coverage of the surface with copper oxide. The decrease in pore radius for the copper exchanged materials as compared to the parent matrix is indicative of copper presence in pores of the lattice. As can be seen from Table 1, the surface area of the CuO catalyst decreased from 289.8 m2/g on HZ (0) to 212.6 m2/g on OXZ (9) with increasing CuO doping from 0 to 8.88 wt%. The total pore volume also reduced from 0.39 to 0.32 cm3/g with increasing metal content. The reduction in pore volume and surface area of the catalyst could be due to the diffusion of metal solution in the pore of zeolite catalysts. As discussed before volume of N2 adsorbed decreases with increasing copper/zinc oxide content due to partial coverage of the surface with copper/zinc oxide [6] & [7]. |
The catalyst treated by oxalic acid has shown higher surface area and pore volume compared to parent 7wt% CuO/HZSM-5 catalyst. It has been reported in literature that mild treatment with oxalic acid leaches out Al of the catalyst, resulting in slight variation in physico-chemical properties of the parent catalyst. Similar trends have also been reported in literature with other catalysts [6]. |
All the catalysts were experimented under identical conditions. For the purpose of comparison mass of the each catalyst, placed in the reactor was 3.0 g using quartz beads as inert diluents and various catalysts were tested for their effectiveness during methanol conversion. All runs were carried out at 673 K and atmospheric pressure. Preliminary experiments carried out with HZSM-5 catalyst at 673 K indicated that C5-C12 hydrocarbons are dominated at these reaction conditions. Preliminary runs were also carried out to study the effect of particle size on methanol conversion and further experiments were made with particles size 2.5±0.5 mm where diffusion effects were negligible. |
There was a significant increase in conversion due to CuO loading. The methanol conversion increased from 38 to 93.7% as CuO loading was increased from 0 to 6.89wt%. Further increase in CuO loading upto 9wt% did not show any improvement in catalytic activity, rather it reduced the conversion of methanol. As the CuO loading was increased from 0 to 7wt%, liquid hydrocarbon yield in the products significantly increased while the yield of C2 and C3 olefins decreased, indicating that alkenes were intermediates. Further increase in CuO loading did not improve the activity of the catalyst possibly due to coverage of the active sites and pore blockage. From Table 2 it can be concluded that the higher hydrocarbons yield and methanol conversion is obtained with OXZ (7), compared to other CuO doped catalysts. Liquid products were also significantly higher. The major products of the reaction were methane, ethylene, propylene, dimethyl ether, pentane, toluene, ethyl benzene, xylene, isopropyl benzene, ethyl toluene, trimethyl benzene and tetra methylbenzene with all these catalysts. All these products were identified from their retention times as obtained by gas chromatography of pure components. The total aromatic hydrocarbons yield increased progressively with increase in wt% of CuO upto 7wt% but further increase in loading to 9wt% decreased the aromatic yield. A comparison of products obtained with various catalysts is given in Table. 2. |
Dimethyl ether obtained from dehydration of methanol generates carbenes and these ions again react with hydrogen and produce methane. Methyl cations react with light olefins to produce higher olefins and these ions again react with higher olefins to form paraffins and dienes. Methanol adsorption may also take place at different acidic and basic sites over the surface of copper impregnated HZSM-5. The acidic sites helps methanol to get converted into DME, olefins and water initially followed by a secondary reaction to form gasoline range hydrocarbons. It was also reported by many researchers that 673 K was the optimum temperature for conversion of methanol to hydrocarbons. At 673 Kthe acidic sites become more energetic due to molecule migration from basic sites to acidic sites and get converted to olefins and finally converted to higher molecular weight hydrocarbons Freeman et al.[2], Haw et al.[8]. It has been reported that the CuO impregnated catalysts have significantly reduced Bronsted acidic sites than that of HZSM-5. The reduction in the Bronsted acid sites is reasonable as these sites are replaced by the metal ions creating new active sites, which are highly selective for gasoline range hydrocarbons. Increasing metal exchange level is the order of decreasing Bronsted acid concentration. |
Effect of run time was also studied to investigate the catalytic activity. It was observed that catalyst with higher wt% of CuO loses its activity faster as compared to lower wt% of CuO Zaidi and Pant [9]. The surface areas and pore volumes of fresh and reacted CuO doped catalysts are given in Table 1.Higher amounts of coke were deposited on the catalyst containing increased loading of CuO. The catalyst loses active sites within the micropore of catalyst and finally micropore gets filled with coke. Effect of run time on conversion and products yield was also studied for CuO doped HZSM-5 and virgin HZSM-5 catalysts by conducting experiment for a run time of 16 h. As can be seen from Fig. 3, conversion of methanol decreased progressively with increase in time on stream. Initial methanol conversion with OXZ (7) and OZ (0) catalysts were 93.72% and 38% respectively. After 16 h run the conversion reduced to 78.7% and 29% respectively with these two catalysts. The decrease in methanol conversion was slower for HZSM-5 as compared to oxalic acid treated CuO/HZSM-5 due to lower active sites over HZSM-5. The total yield of hydrocarbons with respect to time is also shown in Fig. 4. |
The hydrocarbon products yield also decreased with run time. For a run time of 16 h the total product yield reduced from 40.98 wt% to 30.1 wt % on OXZ (7) catalyst. There was a corresponding reduction in conversion and total product yields due to deposition of coke on the catalyst during reaction. The deactivation of catalyst in the transformation of methanol to hydrocarbons is mainly due to coke deposition, which covers the active sites and decreases the active surface area. The surface area and pore volume also decreased with increase in coke deposition over the surface of catalyst as shown in Table 1. After 16 h run under identical conditions physical properties of coked catalysts were also analysed. The typical surface area of OXZ (7) catalyst decreased from 265.7 m2/g to 232.3 m2/g whereas the pore volume reduced marginally from 0.34 cm3/g to 0.33 cm3/g with an increase in coke deposition. |
Top Conclusions Oxalic acid treated 6.89wt% CuO/HZSM-5 produced higher methanol conversion and hydrocarbon yield. Catalyst performance was improved due to elimination of external surface sites via selective delumination of oxalic acid, which results in an easier access of methanol to internal surface sites.The major reaction product were methane, ethylene, propylene, dimethyl ether, pentane, toluene, ethyl benzene, xylene, isopropyl benzene, ethyl toluene, trimethyl benzene and tetra methylbenzene with all these catalysts. |
Top Figures Figure 1.: SEM Photographs of HZSM-5 Catalysts of HZ (OZ)
|  | |
| Figure 2.: Effect of Reaction Temperature on Hydrocarbons Yield [W/FA0 (g cat*h/g of methanol fed)=0.129, P=l atm]
| 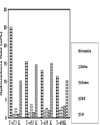 | |
| Figure 3.: Effect of Run Time on Conversion of Methanol, [T=673 K, P=l atm, W/FA0 (g cat*h/g methanol fed)=0.129]
| 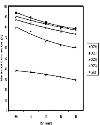 | |
| Figure 4.: Effect of Run Time on the Yield of Total Hydrocarbons, [T=673 K, P=latm, W/FA0(g cat*h/g methanol fed) =0.129]
| 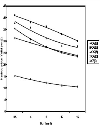 | |
|
Tables Table 1.: Physical Properties of the Catalysts
| Catalyst | Metal content (wt%) CuO | SBET (m2/g) | Pore volume(cm3/g) | | Fresh | Coked* | Fresh | Coked* | OXZ (9) | 8.88 | 212.60 | 170.70 | 0.32 | 0.30 | OXZ (7) | 6.89 | 265.70 | 232.20 | 0.34 | 0.33 | OZ (0) | 0 | 289.80 | 279.20 | 0.39 | 0.35 |
|
| | Table 2: Products Distribution (Yield, wt % feed) for the Conversion of Methanol [T=673K, W/FA0 (g cat*h/g methanol fed)=0.129, P=1 atm]
| Compound | OXZ (9) | OXZ (7) | OXZ (5) | OXZ (3) | OZ (0) | Conversion (%) Yield (wt% feed) | 79.1 | 93.72 | 89.95 | 86.92 | 38.0 | CH4 | 0.45 | 0.34 | 0.40 | 0.92 | 1.0 | C2 | 2.03 | 0.94 | 3.10 | 1.8 | 1.35 | C3 | 2.92 | 0.78 | 1.13 | 2.90 | 3.47 | C4 | 2.28 | 0.71 | 1.49 | 1.94 | 1.89 | C5 | 1.11 | 0.45 | 0.97 | 1.06 | 2.12 | C5+ | 10.11 | 8.09 | 6.50 | 3.30 | 1.0 | C6H6 | 0.05 | 0.15 | 0.18 | 0.02 | 0.27 | C7H8 | 0.22 | 4.36 | 2.60 | 0.93 | 0.72 | C8H10 | 6.09 | 13.20 | 11.66 | 7.30 | 1.10 | C9H12 | 7.09 | 10.80 | 8.26 | 8.95 | 1.10 | C10H14 | 0.17 | 0.33 | 0.40 | 0.75 | tr.* | CH3OCH3 | 2.85 | 0.83 | 1.16 | 1.45 | 1.16 | Hydrocarbon products | (wt % feed) | 35.37 | 40.98 | 37.85 | 31.32 | 15.18 | Water (wt% feed) | 28.40 | 36.10 | 35.20 | 32.20 | 19.38 | Others (wt % feed) | 15.32 | 16.64 | 16.9 | 23.4 | 3.42 |
|
| |
| | |
|
|
|